Projects
ANR RAPHy (2024 - ..)
Hyperstatic Parallel Architecture Robot for Sustainable Industry
Partners : LS2N and Institut Pascal
The aim of this project is to develop a new parallel robot architecture for machining and drilling tasks on large parts or assemblies in the aerospace and shipbuilding industries. This architecture must meet both stiffness requirements and lightweight constraints to minimize the energy consumption required for movement. In this context, the novelty of the project lies in focusing on hyperstatic parallel robots; this type of architecture reduces the weight of moving components while offering high stiffness performance. The design of an industrializable robot involves innovative cross-disciplinary work in scientific fields such as mechanism synthesis, tolerance analysis of hyperstatic mechanisms, and the modeling of the robot’s architecture behavior under the loads induced by hypersticity. The challenge is to control both the behavior and the manufacturing cost of these robots, considering the gains in weight reduction and energy consumption.
Work will focus on validating the choice of architecture for robotic machining. This will involve comparing the performance of different robots with the proposed architectures.

ANR CAP-AM (2024 - ..)
Evaluation and Improvement of Dimensional and Geometric Capability of Multi-Axis Direct Deposition Additive Manufacturing Processes
Partners : COSMER, Université de MONS and Institut Pascal
Additive manufacturing (AM) processes through direct deposition are rapidly developing and address a clear industrial need for the production of large raw parts, within tight deadlines, and in quantities ranging from prototypes to small batches. The use of multi-axis machines allows the manufacturing of complex-shaped parts without the need for support material, which is particularly advantageous for metal fabrication. However, one of the barriers to the widespread adoption of these technologies is the lack of control over quality compared to conventional processes (casting or forging). This concerns the quality achieved in terms of dimensions, geometry, and material properties, depending on the size and morphology of the part to be produced, as well as the manufacturing process parameters. These parameters are related to the deposition process, the production cell (architecture, type, and dimensions of machines/robots), and the methods used (including strategy/path). Mastering dimensional and geometric quality is essential for achieving repeatable raw parts. Knowledge of manufacturing tolerances can therefore be helpful in determining the machining allowances and ensuring the thickness of the remaining raw walls (mechanical strength, mass, etc.). The objective of the CAP-AM project is to develop "tools" for the dimensional and geometric qualification of multi-axis direct deposition AM processes.
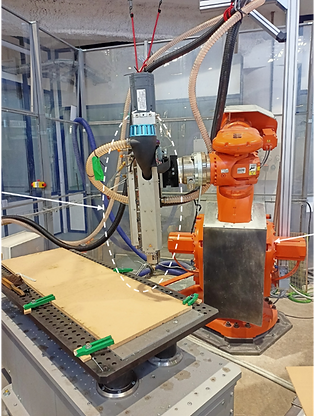
Project CraFT (AURA Region funding) (2021-2026)
Robot Trajectory Calculation for Additive Manufacturing of Complex Tubing
Partners : G-SCOP and Institut Pascal
ANR IMaDe (2019-2023)
Intelligent Machining for Controlling Part Deformation
Partners : LaBoMaP and Institut Pascal
In this project, we focus on controlling the deformation of parts with residual stresses during machining by using in-situ measurement of the part's behavior and proposing an intelligent adaptation of the clamping system. This project contributes to the development of so-called intelligent machining, tailored to the part’s behavior both during machining and after de-clamping.
To achieve this goal, we are conducting research around two major scientific challenges:
-
The development of a quantitative imaging measurement method suitable for machining large parts by combining stereo-correlation and image projection. The goal is to determine the absolute displacement of the part's general shape relative to the machining reference system and the positions of functional surfaces within the part's reference system.
-
Controlling dimensional defects generated by the rebalancing of residual stresses through intelligent machining setups. By coupling the forces measured at the clamps, the part's deformation measurement, and a meta-model developed within this project, we aim to estimate in real-time the final deformation of the part after de-clamping. This work will help propose a strategy for reducing defects, particularly through the adaptation of the machining setup.
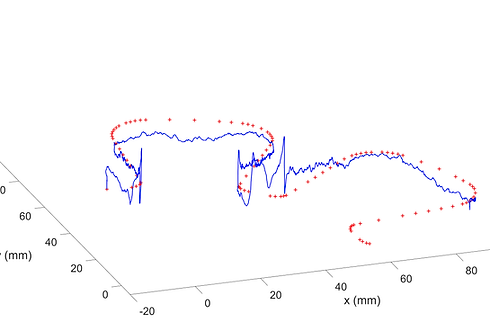
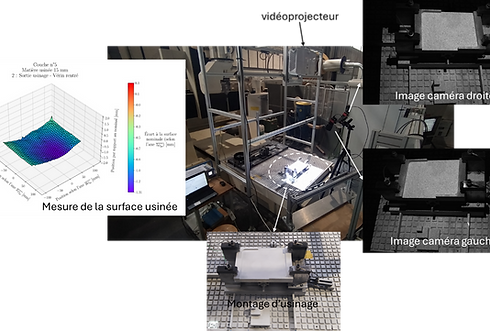